- Industry
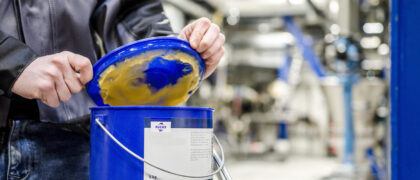
The automotive industry is the driving force of the **Polish economy and an important GDP-generating branch. The figures speak for themselves. The automotive parts industry and market sector generates PLN 140 billion in turnover annually*, and Poland is one of the top ten global exporters of parts.
**Please add here information about your local market.
When we speak of the automotive industry, we mainly mean the plants assembling vehicles, e.g. **in Tychy, Gliwice, Poznań, Września, Jelcz, etc. However, it is worth knowing that as many as 80% of jobs in the automotive industry are concentrated in the production of car parts and accessories, e.g. in Wałbrzych, Bielsko, Tychy, Poznań, Mielec, Gliwice, Kielce, Skawina and many others.
Companies producing car parts and accessories are developing exceptionally dynamically and making increasingly bold use of modern technologies. As a result, they are producing increasingly robust components from modern steels and non-ferrous metal alloys.
However, in order for the plant to operate efficiently, the right lubricants must be selected for these specialised materials. The tasks of such preparations include:
It is also important that the lubricant can be easily removed from the surface of the moulded parts in a typical industrial washing process.
But which specific product should you opt for? In our opinion, the lubricants from the innovative RENOFORM series deserve special attention.
The task of developing modern lubricants that meet these requirements is taken on by the research and development laboratories of the lubricant manufacturing industry.
An example of this are FUCHS laboratorie, whose close cooperation with plants producing automotive parts and accessories has resulted in a number of industry-appreciated lubricants from the RENOFORM series. These are used to form steel components, machine parts and accessories for the automotive industry.
A particularly recommended product that brings tangible benefits to customers producing parts and accessories is FUCHS RENOFORM DMO 5035. It is used in the manufacture of steel parts shaped by forming operations: punching, stamping and thread extrusion, among others. For business customers, it is available in large 205 L drums.
At one of our customers, the traditional lubricant was causing typical wear on the surface of the tools and they had to be replaced after 800 items produced. This caused increased costs, because in addition to having to recondition the tools, production had to be stopped for the duration of the replacement. This caused unnecessary standstills.
Another solution was needed to guarantee greater savings. The state-of-the-art FUCHS RENOFORM DMO 5035 came to the rescue.
Its application translated into less wear and tear and an increase in production capacity of up to 6,000 parts between mould tool changes. In addition, the customer counted easier washing after the moulding operation among the benefits.
It is always worth bearing in mind that the precise selection of a lubricant results in concrete financial benefits for the production plant. And all the above-mentioned advantages make the product FUCHS RENOFORM DMO 5035 synonymous with excellent cooperation between parts manufacturers and lubricant manufacturers.
1 According to the Association of Automotive Parts Distributors and Manufacturers